Double Roll Crusher: Suitable Materials and Key Considerations
Double roll crushers utilize two counter-rotating rollers to crush materials through compression and grinding. They are ideal for medium- to low-hardness materials (Mohs hardness ≤ 8) with high brittleness.
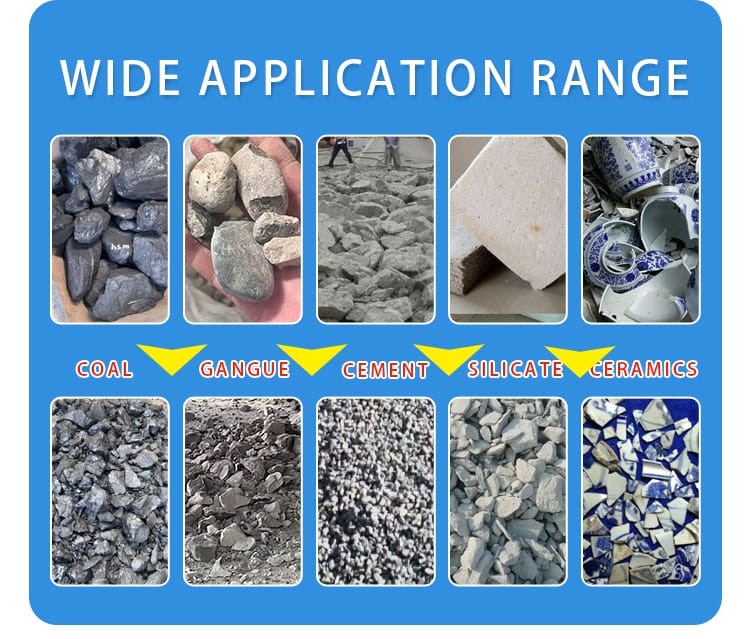
Double Roll Crusher Applicable Material Types
- Coal and Coke
- Reason for Suitability: Medium hardness and high brittleness make coal and coke easy to crush via roller compression, commonly used in coal mines and coking plants.
- Non-metallic Ores
- Examples: Limestone, gypsum, dolomite, marl, sandstone.
- Applications: Raw material processing for construction materials and chemical industries.
- Metallurgical Waste
- Materials: Sintered ore, blast furnace slag (moderate hardness), metal silicon slag.
- Caution: High-hardness metallurgical waste (e.g., some slags) may accelerate roller wear; regular maintenance is required.
- Construction and Chemical Raw Materials
- Construction Sector: Cement clinker (secondary crushing), quartz sand, feldspar.
- Chemicals: Phosphate rock, potash salts, pyrite, where uniform particle sizing is critical.
- Glass and Ceramic Raw Materials
- Examples: Quartz, feldspar (primary crushing of brittle materials), provided moisture content is controlled to prevent roller sticking.
Key Limitations
- Avoid Processing:
- High-hardness materials: Granite, basalt (Mohs hardness >8), which damage roller surfaces.
- Adhesive or high-moisture materials: Wet clay or viscous substances may cause blockages.
- Ultrafine grinding requirements: Minimum discharge size typically ≥2mm; finer outputs require ball mills.
- Equipment Parameters:
- Feed size: Generally ≤25mm (dual-roll) or up to 50mm (quad-roll crushers).
- Discharge size: Adjustable via roller gap, typically 2–10mm.
Selection Guidelines
- Material hardness: Evaluate using the Mohs scale.
- Roller surface material: Choose high manganese steel, tungsten carbide, etc., based on abrasion resistance needs.
- Design features: For sticky materials, opt for rollers with scrapers or toothed surfaces to improve throughput.
Ensure alignment with production capacity requirements (e.g., motor power, roller diameter) and operational conditions (e.g., moisture content). Technical specifications should be cross-checked with manufacturers for optimal performance.